MU3/MORSØ Faceframe
Hoffmann and Morsø
….the solution to profitable face-frame construction is here!
The Morsø NF series of guillotine style notching machines are specifically designed for the fast and accurate processing of beaded face-frame stiles and rails. The manual machines are operated by depressing a foot pedal and by moving a hand lever to control the cutting head. Please watch the video below to see how simple the process is.
Notching Operation (stiles)
Coping Operation (rails)
Upon adjusting the cock-bead stops to set the notching depth, the moulding is placed on the machine table and one end is rested against a flip stop. The hand lever in front is used to move the cutting head horizontally to and from the operator.
Depending on the width of the cut and the thickness and hardness of the moulding, two to four cuts are made to complete the notch.
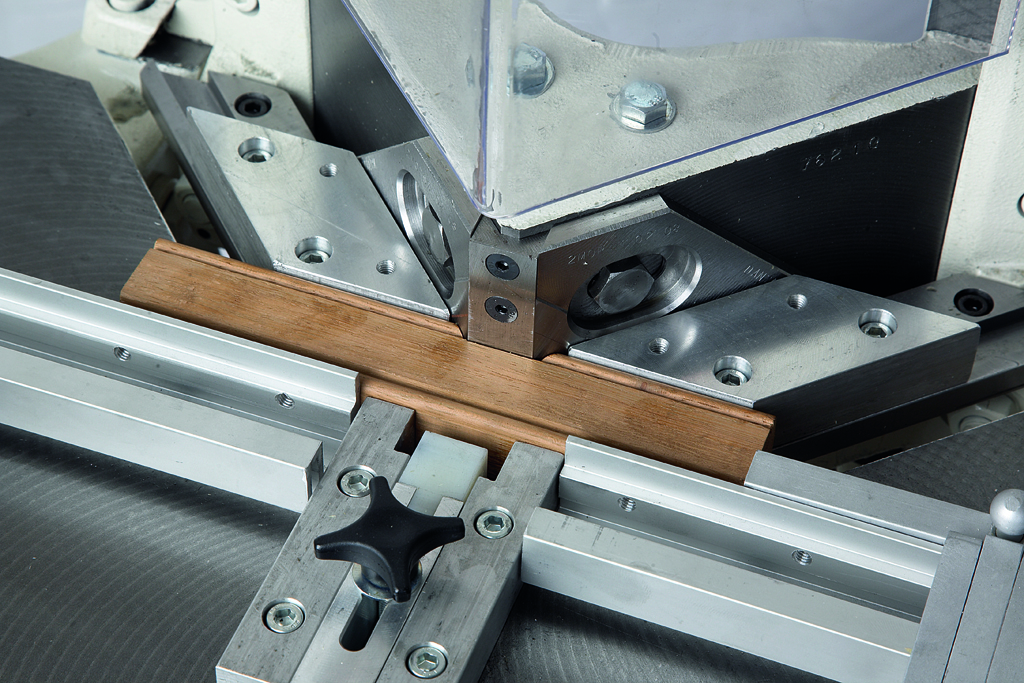
The rail is placed on the table and pushed against the centre stop. The 45-degree corner cut on the bead is made in one cycle, multiple cuts are not necessary.
Morsø Models
NFS; manual, foot operated machine for up to 70mm wide moulding fitted with nose widths of 6 – 20mm
NFl; manual, foot operated machine for up to 70mm wide mouldings fitted with nose widths of 12 – 26mm
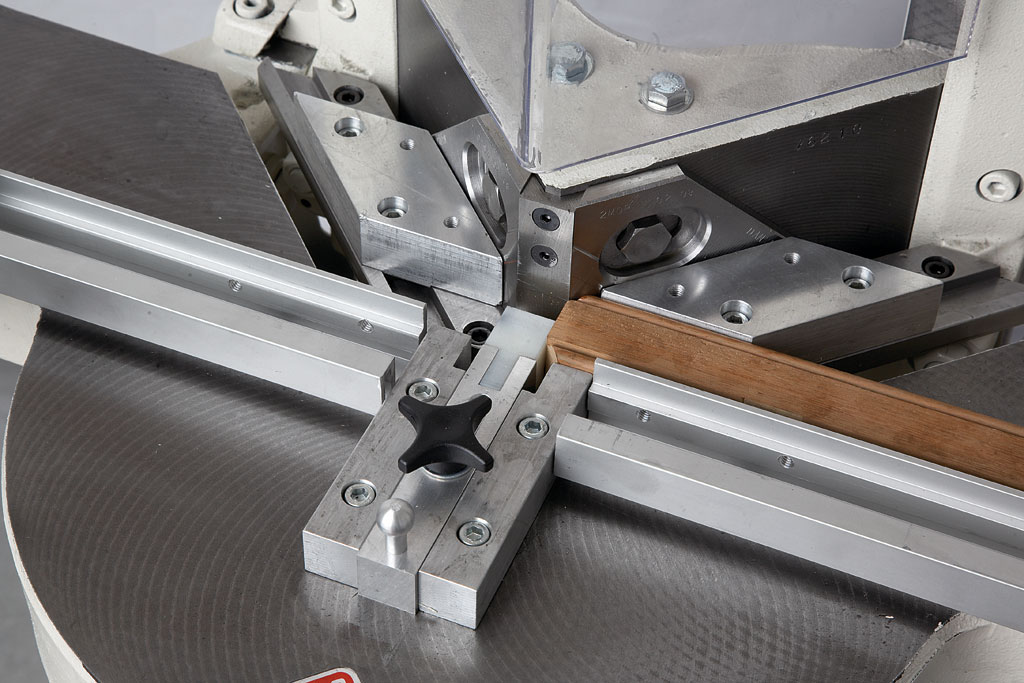
Routing Operation
Aside from being used for mitre joints, butt joints, compound mitres etc, the machines can also accurately rout keyways into bead moulded notch joints.
The moulding is placed on the machine table and positioned with the fixtures, then the router bit is raised up from below the table until the pre-set routing height is reached. This operation is either done manually by pulling on the main lever on the MU3 models, or by stepping on the foot pedal of the automatic MU3P.
When two parts are drawn together using a Hoffmann key, a precise, durable and accurate joint is produced without the aid of clamps or alignment jigs.
The Benefits
The Hoffmann Beaded Face Frame System offers cabinet and millwork shops of all sizes a fast, precise and efficient way to manufacture beaded face frames, whether it’s one or one hundred frames per job. Starting with beaded moulding, the stiles are notched and the rails are coped on a fixed-blade, guillotine style notching machine.
A second step takes place on a Hoffmann dovetail routing machine equipped with special fixtures for the notched material. Dovetail keyways are routed in all mating parts and the frames are assembled simply with glue and Dovetail Keys. No large clamping tables or bar clamps are required, the frames can be sanded and finished immediately upon assembly.
All dovetail routing machines are set-up with a complete fixture set to process stiles and rails, but can also be used to process regular mitre joints and butt joints.